What is Porosity in Welding: Key Variables and Their Influence On Weld High Quality
What is Porosity in Welding: Key Variables and Their Influence On Weld High Quality
Blog Article
The Science Behind Porosity: A Comprehensive Guide for Welders and Fabricators
Comprehending the complex systems behind porosity in welding is crucial for welders and fabricators striving for remarkable craftsmanship. From the make-up of the base products to the intricacies of the welding procedure itself, a multitude of variables conspire to either exacerbate or reduce the existence of porosity.
Comprehending Porosity in Welding
FIRST SENTENCE:
Assessment of porosity in welding exposes vital understandings into the honesty and top quality of the weld joint. Porosity, defined by the visibility of dental caries or spaces within the weld steel, is a common problem in welding processes. These spaces, if not correctly dealt with, can jeopardize the structural honesty and mechanical buildings of the weld, resulting in prospective failures in the finished product.
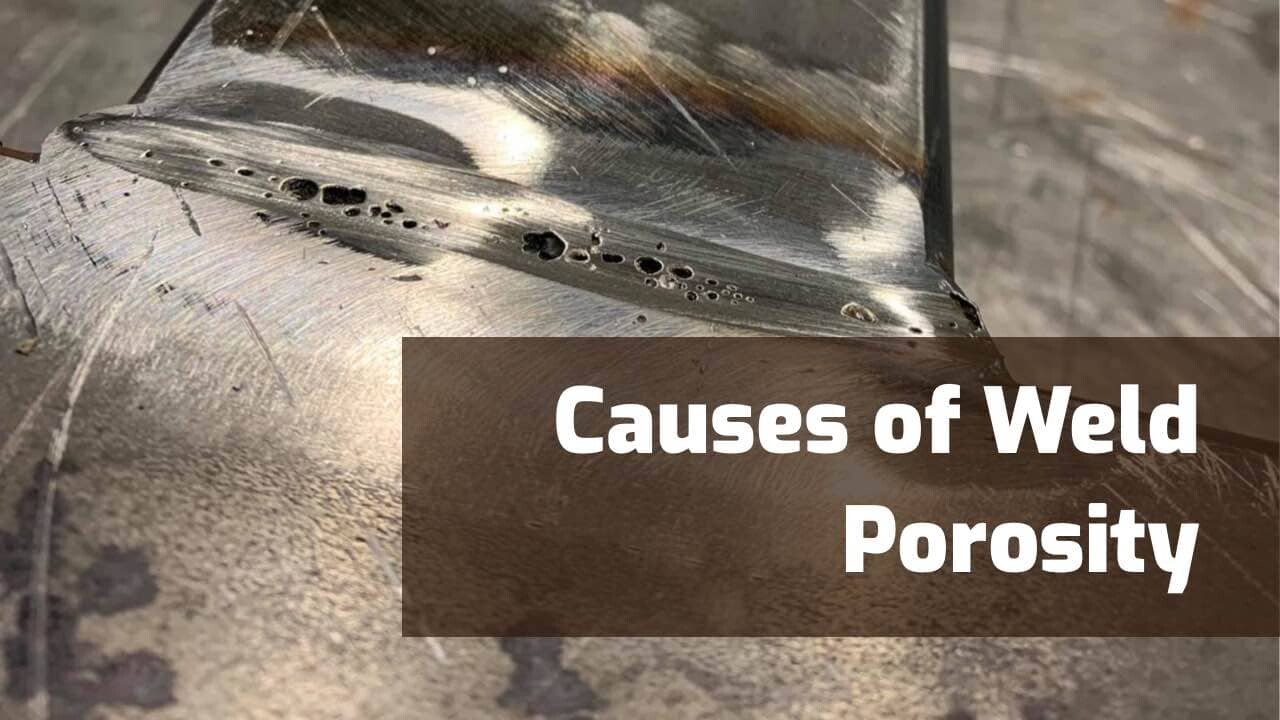
To discover and measure porosity, non-destructive testing approaches such as ultrasonic screening or X-ray evaluation are frequently employed. These techniques permit the recognition of interior flaws without compromising the honesty of the weld. By analyzing the dimension, form, and distribution of porosity within a weld, welders can make informed decisions to boost their welding processes and accomplish sounder weld joints.

Variables Affecting Porosity Development
The incident of porosity in welding is affected by a myriad of elements, varying from gas protecting efficiency to the complexities of welding criterion settings. Welding specifications, consisting of voltage, current, take a trip speed, and electrode type, also effect porosity formation. The welding method utilized, such as gas steel arc welding (GMAW) or protected steel arc welding (SMAW), can influence porosity formation due to variations in heat circulation and gas coverage - What is Porosity.
Effects of Porosity on Weld Quality
The presence of porosity likewise compromises the weld's resistance to rust, as the entraped air or gases within the voids can react with the surrounding setting, leading to destruction over time. Additionally, porosity can hinder the weld's capability to endure stress or impact, additional endangering the general quality and reliability of the bonded framework. In critical applications such as aerospace, automotive, or structural constructions, where safety and toughness are vital, the detrimental impacts of porosity on weld quality can have extreme repercussions, emphasizing the importance YOURURL.com of minimizing porosity with proper welding strategies and treatments.
Strategies to Lessen Porosity
Additionally, utilizing the proper welding parameters, such as the appropriate voltage, current, and travel speed, is crucial in avoiding porosity. Preserving a regular arc size and angle during welding likewise assists decrease the probability of porosity.

Additionally, choosing the ideal shielding gas and keeping proper gas circulation prices are necessary in decreasing porosity. Using the appropriate welding strategy, such as back-stepping or using a weaving movement, can also assist distribute warm evenly and decrease the opportunities of porosity development. Making sure correct ventilation in the welding environment to click site eliminate any type of prospective resources of contamination is essential for accomplishing porosity-free welds. By implementing these strategies, welders can successfully decrease porosity and create premium welded joints.

Advanced Solutions for Porosity Control
Carrying out sophisticated modern technologies and cutting-edge approaches plays a crucial role in attaining remarkable control over porosity in welding processes. One innovative option is using innovative gas blends. Protecting gases like helium or a mix of argon and hydrogen can assist decrease porosity by providing far better arc security and enhanced gas insurance coverage. In addition, utilizing advanced welding methods such as pulsed MIG welding or changed atmosphere welding can also assist alleviate Your Domain Name porosity issues.
Another innovative service entails using innovative welding tools. Utilizing equipment with integrated functions like waveform control and advanced power resources can improve weld high quality and lower porosity threats. The implementation of automated welding systems with exact control over parameters can significantly decrease porosity issues.
In addition, incorporating sophisticated monitoring and assessment innovations such as real-time X-ray imaging or automated ultrasonic testing can assist in finding porosity early in the welding procedure, permitting for prompt rehabilitative activities. Overall, integrating these innovative services can considerably improve porosity control and enhance the overall high quality of welded parts.
Final Thought
To conclude, recognizing the science behind porosity in welding is essential for welders and makers to generate top quality welds. By recognizing the variables affecting porosity development and applying strategies to reduce it, welders can improve the overall weld top quality. Advanced remedies for porosity control can further enhance the welding procedure and make sure a solid and trusted weld. It is essential for welders to continually enlighten themselves on porosity and carry out finest techniques to accomplish optimal results.
Report this page